Equipment
Production Equipment
At Tejas Production, we offer comprehensive production equipment and services to meet the needs of our oilfield customers. With a 22-acre manufacturing facility full of high-tech welding and assembly stations, a 45-foot plasma table and two rolling machines that can roll up to 3.5″ thick steel, we are well positioned to provide you with the latest in production technology.
Our new equipment fabrication, used equipment sourcing and refurbishing, as well as component prepping capabilities are second-to-none. We specialize in plate rolling and welding, CNC plasma cut parts, and band saw-cut pipe for all your production requirements. We also feature five-, 30-, and 40-ton overhead cranes for loading and shipping your orders on time.
Additionally, Tejas Production offers aftermarket services such as comprehensive field maintenance, service packages, and equipment refurbishing services so you can keep your oilfield operations running smoothly. We strive to provide you with the utmost safety in all our operations while delivering top quality products at competitive prices. Our commitment to customer satisfaction is unmatched – contact us today to learn more about how Tejas Production can help optimize your production needs!
Core Products
Core Products
Used Equipment
Used Equipment
Component Prep
Component Prep
Aftermarket Services
Aftermarket Services
NEW EQUIPMENT FABRICATION
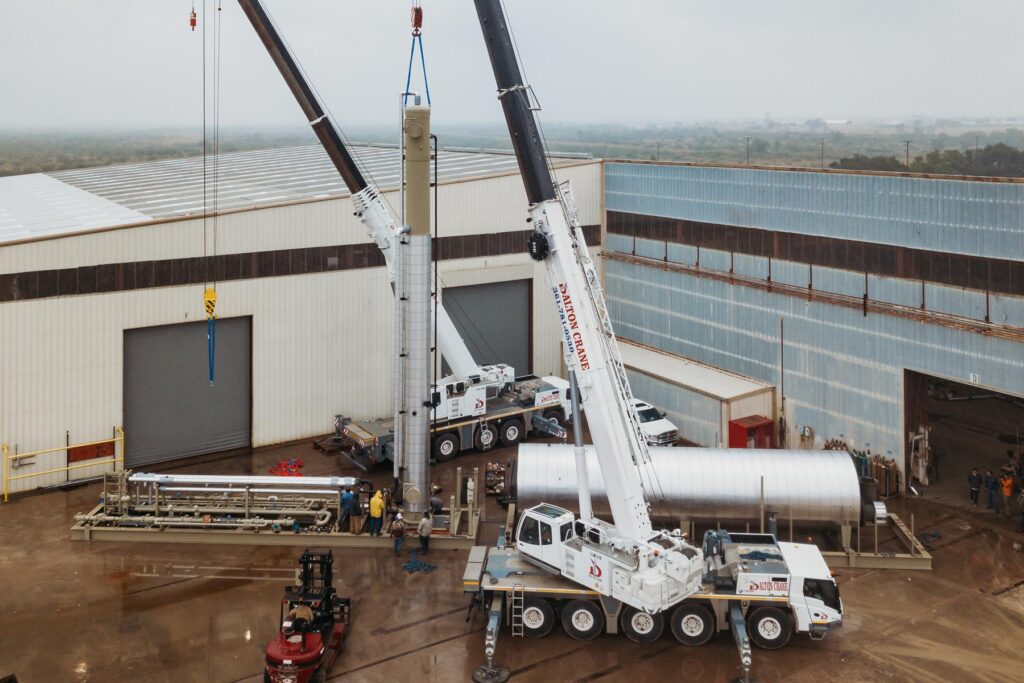
Gas Dehydration Units (5-150 MMSCFD)
Glycol Dehydration units remove entrained water vapor from natural gas streams for various reasons, but they are primarily used to meet sales takeaway specifications, reduce the amount of free liquid fallout, and prevent hydrate formation and corrosion in pipelines.
Tejas Production Service’s glycol dehydration modular unit is a reliable, efficient system for removing water from natural gas well streams in order to meet typical pipeline and process specifications. Multiple stages of removal are contained on a single skid-mounted unit, giving you a wide range of options and flexibility to configure the system to your specific application. Tejas Production Services has proven designs sized from .500 mmbtu to over 2.0 mmbtu.
How it works
Wet gas enters the bottom of the absorber tower and ascends through a mist extractor where fine liquid particles are removed. As the gas rises through the tower’s packing or bubble cap trays, water is absorbed by descending lean glycol (water removed through the regeneration process), which is continually pumped to the top of the tower. Drier gas exits the top of the tower and passes through the glycol/gas heat exchanger to the gas outlet. The rich glycol (wet with absorbed glycol) collects in the hat tray at the bottom of the tower and flows to the power side of the glycol pump. From the pump, the rich glycol flows through a reflux coil, heat exchanger, and flash gas separator, which divides gas and entrained hydrocarbons from the glycol. The gas then flows to the fuel gas scrubber and the lean glycol flows through a filter into the reboiler. As the reboiler drives off water vapor through the still column, the hot, reconcentrated glycol flows from the reboiler to the sparger box to remove additional water vapor. The lean glycol flows to the storage compartment and then to the heat exchanger for cooling. The cooled, lean glycol then flows through a glycol sock filter before passing to the glycol pump. Lean glycol and gas from the absorber together power the glycol pump, which pumps the glycol through a glycol/gas heat exchanger to minimize glycol loss and then to the absorber tower to continue the dehydration process cycle.
Oil Stabilizers
How it works
After upstream separation, the condensate stream enters the unit. It is first preheated in the inlet heat exchanger and then flows into the upper section of the stabilizer tower. Inside the tower, the light components – typically methane, ethane, propane, and butane – rise and exit the overhead vapor outlet. The heavier liquid components descend and pass through the indirect heater to cause additional vapor to flash off, rise and exit the tower. Stabilized liquids collect in the bottom of the tower. They are routed to the inlet heat exchanger to cool. Stabilized liquid product then flows to storage tanks. The vapor that exits the tower flows through an ambient cooler and then to a low-pressure separator. Gas from the separator is routed to compression for delivery to market. NGLs exit the separator and flow to a blowcase where they are pressurized for a bullet tank or pipeline.
Bulk & Test Separator Skids
Gas Production Units
How it works
A high-pressure production stream will enter the GPU where it will initially be heated before and after flowing through a pressure-reducing choke to prevent freezing of hydrates and condensates entrained in the stream. Once it is heated and the pressure is reduced, the production stream enters the separator where liquids and natural gas are separated. The gas flow will rise to the top of the vessel, while the liquids will drop and exit the bottom of the vessel.
Gas & Liquid Filtration
Filter Separators are designed for high gas flow/ low liquid volumes specifically for the removal of particles, mist, fogs, rust and dust from gas streams. These contaminants usually exist with the bulk of the particles having diameters considerably less than 10 microns; therefore, filter separators are preferred since standard separators or scrubbers have difficulty in effectively removing these very small particles. Tejas Production Services offers a dual sump design with 1 micron filters to effectively eliminate these small particle from gas streams up to 200 mmscf/d at 1400 MAWP. Filter separators containing .3 micron filters are used for the removal of lube oils and other contaminates. Filter Separators are typically employed upstream and downstream of natural gas compressors, glycol dehydration units and fuel gas applications.
How it works
Tejas Production’s proven design is a horizontal vessel containing two sections and two liquid boots. The first section contains the filter elements for the removal of solid particles. The second section contains a mist extractor for the removal of any liquid droplets down to approximately 10 microns. The gas flow enters the first section and flows through the filter elements from the outside to inside where the solid particles are removed. The gas then travels through the inside of the element to the second section where the liquid particles can be removed through the mist extractor. Filtered gas then exits the vessel and the liquids fall into the liquid boots where they are discharged from the vessel by means of an automatic level controller and level control valve. Tejas Production Services also includes differential pressure gauges on both sides of the filter element to show when it is time to replace the filter element.
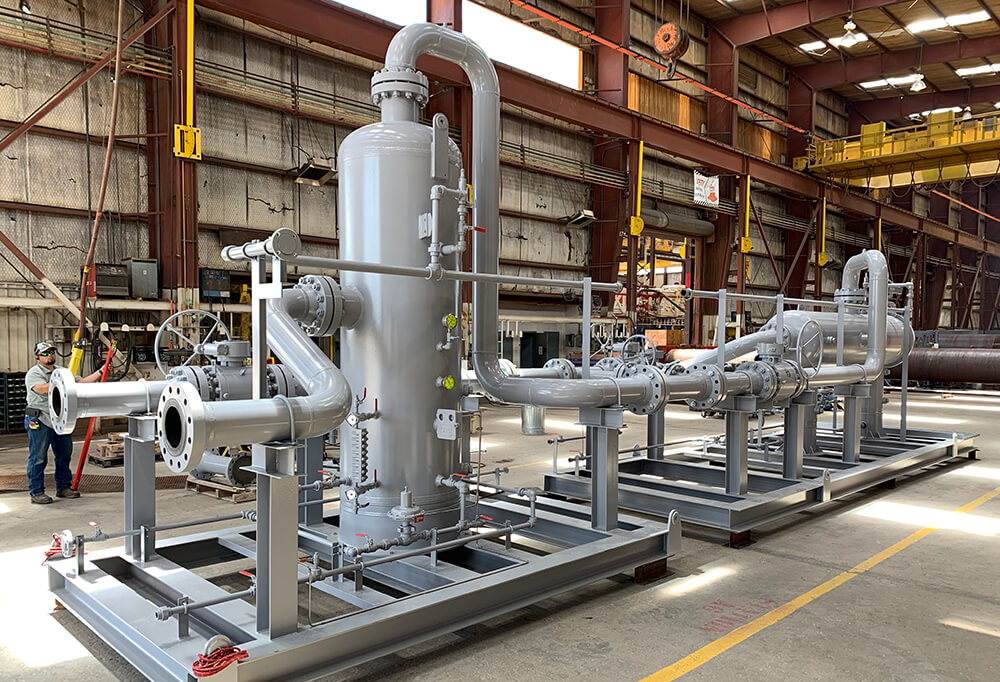
Forced-Draft Coolers
How it works
The cooling process is achieved by the flow stream entering multiple exchangers that are cooled by a fan blowing air across the tubes. The fan is driven by a gas engine or electric motor.
JT (Joule-Thomson) Skids
Tejas Production Services’ JT (Joule-Thomson) modular skids are commonly used for several services (1) dewpoint pipeline control to meet pipeline specifications and (2) fuel conditioning to lower the BTU content of fuel gas to meet engine or equipment specification. Tejas JT skids are self-contained and compact, minimizing valuable site easement and access. Skids include inlet gas/outlet gas exchanger, inlet gas/NGL exchanger, temperature-controlled hot gas bypass control, JT expansion valve, methanol pump, and a NGL recovery separator. Tejas Production Services standard sizes are .500, 1, 3, 5, and 10 mmscf/d.
How it works
Gas enters the Tejas JT skid at high pressure and travels through a gas to gas heat exchanger and then a gas-liquid heat exchanger. The gas then passes through the Joule Thomson valve, taking a pressure drop and cooling down to a low of -20°F. Liquid fallout after the Joule Thomson valve is collected in the cold separator and sent to storage tanks or other processes at the facility site. The cold gas then travels back through the heat exchanger and exits the JT plant. JT skids typically require a hydrate inhibitor to be injected to prevent freezing and hydrate formation. Methanol is commonly used but cannot be recovered and leaves with the exiting lower BTU gas outlet stream.
Fuel Gas Skids
Tejas Production Services Gas Conditioning skids reduce the BTU of the gas stream and protect gas-fueled engines, turbines, and instrumentation systems. They are designed as a compact, integrated, skid-mounted system that is easily added to an existing facility with high BTU fuel gas issues. Tejas Production Services standard sizes are 1,3, and 5 mmscf/d.
How it works
A high-pressure gas stream enters the skid through dual high-pressure regulators. The gas then goes through a second parallel set of lower pressure regulators. The downstream separator allows free liquids to fall out and be removed from the gas stream. The downstream gas stream has a lower BTU level for your application.
Separators
Tejas Production Services designs and builds a variety of ASME coded separators in both vertical and horizontal orientations and in Phase 2, 3, and 4 styles. These “vessels” can be designed to meet customer-specific dimensions to almost any OD or length, and pressure ratings from 125 – 5000 psi. A few examples that Tejas fabricates are scrubbers, slug catchers, freewater knock-outs, vapor recovery towers, test and allocation assemblies, blowcases, sand separators, flare knock-outs, feed separators.
Separators are used to collect and separate oil, gas, and water through a certain amount of retention time. Horizontal separators are typically used for applications where large amounts of liquids are expected. Vertical vessels are typically used for applications where large amounts of gas are expected, or there are space constraints.
How it works
A combination of oil, gas, and water will flow into the inlet part of the separator, where it will initially hit the inlet deflector, causing the separation of gas from liquid. The liquid will fall to the bottom of the vessel, while the gas rises to the top of the vessel. In the second phase of separation, the larger liquid particles fall out from the gas with an extended amount of time known as retention. Next, the gas will flow upward and exit through a mist/vane extractor before exiting the outlet of the vessel where liquid particles entrained in the gas will fall out. Lastly, natural gas exits the top of the vessel, and liquids will exit the bottom of the vessel.
Coalescing Filter Separators
Tejas Production Services has a proven design to remove liquid contaminants and particles greater than 0.3 microns from the natural gas stream. Tejas’s reverse flow gas coalescer uses inside to outside elements to cause larger liquid droplets to form. By collecting these larger droplets of particulates, the coalescing filter protects expensive downstream equipment from contamination such as glycol dehydration units and processing plants.
How it works
Tejas Productions standard coalescing filter is a vertical vessel containing two chambers. The lower inlet chamber is used as a free liquid integral scrubber. The upper chamber contains the mounted coalescing elements on standpipes. The gas flow enters the lower chamber where any free liquids will drop out of the gas stream to be removed via a level control and dump valve. The gas stream then travels upward into the coalescing elements inside to outside. The element forces small liquid particles to agglomerate (coalesce) forming larger drops or particles as it progresses through the element. The resulting larger droplets fall to the bottom of the upper chamber to be removed via a level control and dump valve. The gas stream then flows out through the side separator section. This design can have a liquid removal efficiency of 0.3 micron can be obtained.
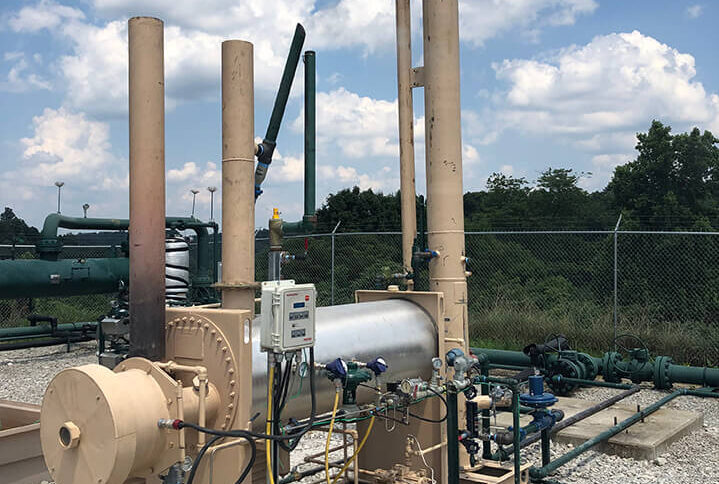
Heater Treater & Heated Separators
How it works
A combination of oil, gas, and water will flow into the inlet part of the heated separator and treater, where it will initially hit the inlet deflector, causing the separation of gas from liquid. The diverted flow will fall and travel through the vessel while simultaneously being heated through its direct contact with the firetube. The water will descend to the bottom, while the oil will remains in the middle, and natural gas will flow upward through the vessel.
Slug Catchers
Slug catchers are large vessels designed to catch large quantities of liquids, commonly used at the receiving side of a pipeline pigging operation.
Tejas Production Services slug catchers (skid-mounted and packaged or bare vessels) can be custom created in a horizontal orientation, with pressure ranges from 500 – 1440 w.p., and sizes from 48 O.D.” x 20’ Length to 180” O.D. x 80’ Length.
Line Heaters
During the natural gas and oil stream processes, continuous fluctuations in temperature and pressure can result is production and equipment issues downstream.
Line heaters are water bath indirect heaters, designed to safely heat a gas and, or oil stream flow, and are commonly used to take a pressure drop after the well head.
Tejas Production Services can custom fabricate line heaters to customer-specific dimensions. Ranging is sizing from 250,000 BTU Hr and 24” O.D. x 7’6” in length to 2,000,000 and 60” O.D. x 20’ in length.
Heater Skids and Pipe Racks
Pipe racks are utilized to support pipes, cable trays, power cables and more in industrial settings. Often times pipe racks also support mechanical equipment, valve access platforms and vessels.
Other Skid-Mounted Modular Production Equipment
Tejas Production Services has a proven design to remove liquid contaminants and particles greater than 0.3 microns from the natural gas stream. Tejas’s reverse flow gas coalescer uses inside to outside elements to cause larger liquid droplets to form. By collecting these larger droplets of particulates, the coalescing filter protects expensive downstream equipment from contamination such as glycol dehydration units and processing plants.
How it works
Tejas Productions standard coalescing filter is a vertical vessel containing two chambers. The lower inlet chamber is used as a free liquid integral scrubber. The upper chamber contains the mounted coalescing elements on standpipes. The gas flow enters the lower chamber where any free liquids will drop out of the gas stream to be removed via a level control and dump valve. The gas stream then travels upward into the coalescing elements inside to outside. The element forces small liquid particles to agglomerate (coalesce) forming larger drops or particles as it progresses through the element. The resulting larger droplets fall to the bottom of the upper chamber to be removed via a level control and dump valve. The gas stream then flows out through the side separator section. This design can have a liquid removal efficiency of 0.3 micron can be obtained.
USED EQUIPMENT
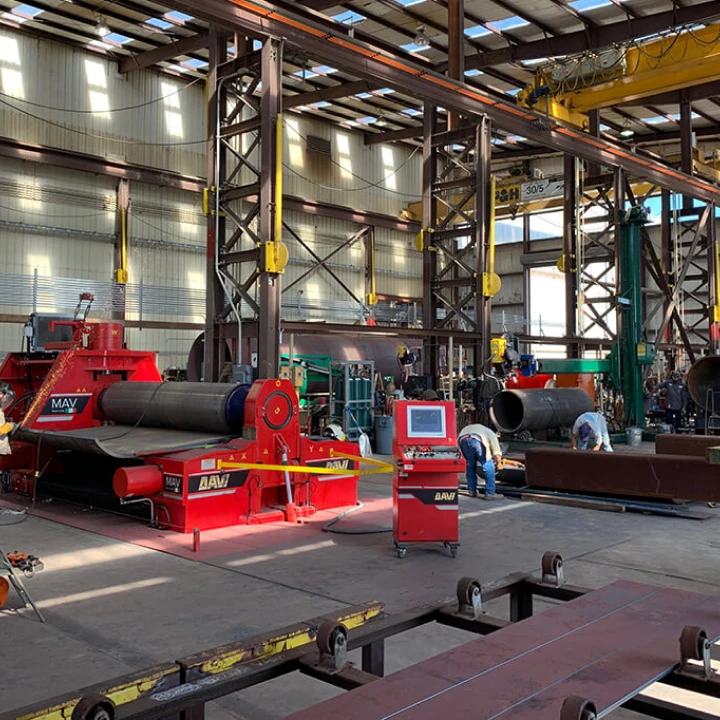
COMPONENT PREP
CNC Plasma Cut Parts
Tejas is equipped to supply ASME certified vessel shells and plasma-cut plate parts with industry-leading delivery times. This gives you the competitive pricing, quality and production efficiency you require.
Plate Rolling & Welding
Your shells and piece parts will be cut by an HD articulating/beveling plasma table, then rolled on one of two plate rollers, capable of rolling .25”-3.5” thick shells, and finally, seamed with one of four sub-arc welding machines.
Band Saw-Cut Pipe
You can also get your piece parts such as legs, repads, internal parts, plate flanges, firebox flanges, lift lugs, fire tube and more cut by Tejas for a fraction of the cost and time of doing so by hand. Our band saw can cut up to 20” pipe at the exact angle you need. Tejas Production Services is proud to supply the vessel materials you need, when you need them!
Aftermarket Services
Tejas Production offers aftermarket services such as comprehensive field maintenance, service packages, and equipment refurbishing services so you can keep your oilfield operations running smoothly. We strive to provide you with the utmost safety in all our operations while delivering top quality products at competitive prices. Our commitment to customer satisfaction is unmatched – contact us today to learn more about how Tejas Production can help optimize your production needs!
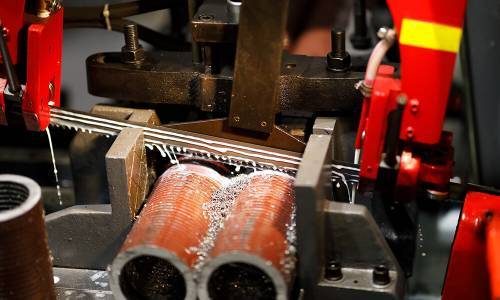